Design and manufacture of refinery production line equipment
Foulad Machine Delijan
Delijan Machine Steel Company by using committed and expert engineers and by creating cooperation and technical partnership corridors, while taking advantage of the potential of large design companies and Iranian and foreign contractors, the ability to design and manufacture refinery equipment and devices related to the oil industry such as:
- Heat exchanger (Shell & Tube)
- Piping
- Furnace
- Storage Tank
- Valves
1-Heat transformer
In industrial processes, the waste of heat and energy causes an increase in fuel consumption and causes deficiencies in the system. Heat exchangers increase the efficiency of the system by maximizing the efficiency of heat transfer between two different fluids, while preventing heat loss.
Heat exchangers, while providing the possibility of hot liquid passing by cold liquid without the risk of mixing with each other, enable heat transfer. Heat is transferred from hot liquid to cold, cold liquids are heated and hot liquids will naturally cool down. Therefore, heat is not lost during the heat energy transfer operation in these devices.
One of these two fluids passes through a narrow tube and the other fluid surrounds the tube. There are different types of heat exchangers and the most suitable model can be chosen according to the user characteristics of the system.
Generally, heat exchangers can be divided into three general categories:
1- Parallel flow converters include two different liquids that enter the converter from one side and flow in the same direction.
2-In opposite or asymmetrical heat exchangers, the cold liquid enters the exchanger from one direction and the hot liquid from the other direction and passes by each other. These converters are more efficient in heat transfer than other models.
3- In the crossover heat exchanger, hot and cold liquids meet each other vertically, and heat is exchanged at the intersection.
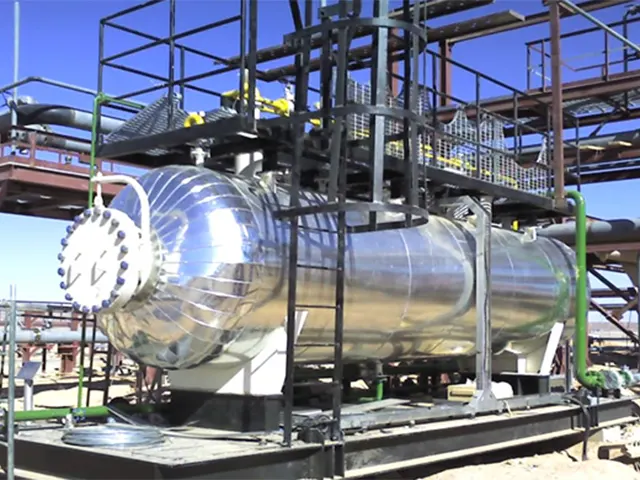
2-Piping
One of the safe and cost-effective ways in production systems to transfer liquids between equipment is to use pipelines. The material used in piping lines can be different depending on the type of materials that are being transported and of course the environmental conditions. The material of these pipes can be steel, cast iron, carbon steel, plastic, etc. Pipes of the piping system are usually connected to each other with flanges or by welding.

Important standards in the piping system
API 570, Piping Inspection Code (Inspection, Repairs, and Alterations in Piping System Service). This standard is a good guide to determine which piping is most compatible with CUI.
API RP 574, Inspection Method for Piping System Components. This standard examines the method of inspection of piping, tubes, valves and fittings.
API RP 578, approval of new and existing materials in the piping system. Guidelines for Material and Quality Assurance in Piping System Alloy Compatibility.
API RP 583, Corrosion Under Insulation and Fireproofing, Covering Design, Maintenance, Inspection, and Methods for Handling External CUIs Applicable to Pressure Piping, Storage Tanks, and Furnaces.
ASME PCC-2, Repair of Pressure Equipment and Piping, Methods for Repair of Equipment and Piping within the Scope of ASME Pressure Technology Codes.
ASTM STP 880, Corrosion of Thermally Insulating Metals, which provides information on corrosion problems in thermally insulating equipment and piping components when the components become wet.
3-Pipeline or pipelines
There is a major difference between pipelines and piping and that is that pipelines are used to transport materials over a long distance between two separate systems, while the piping system is used to transport gases and liquids such as water or chemicals in an industrial unit.
Pipelines consist of metal and plastic pipes of various sizes that are used to transport crude oil, refined petroleum products, and liquefied natural gas from production areas to refineries and other technology companies. These liquids are transferred using pumping stations that are placed alternately along the pipeline.
4- Storage tank
Storage tanks are large tanks that are usually made of metal and have different types and are usually installed on the ground. These tanks are designed to temporarily store petroleum, chemical, water, or various gases.
Depending on the type of materials and environmental conditions, such as pressure and temperature, storage tanks are made in various shapes and materials, and sometimes they are insulated for different uses and its design and construction is accompanied by hot oil coils to keep heavy materials warm.
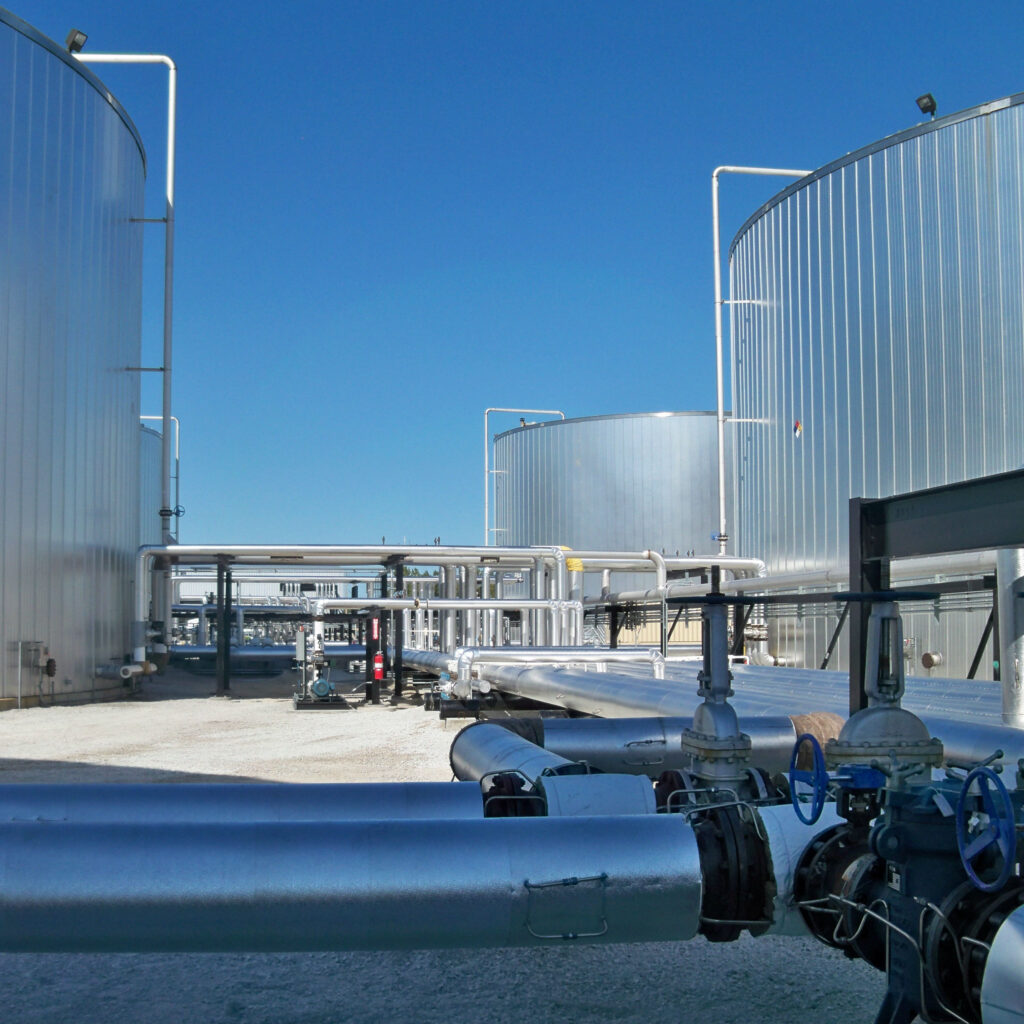
5- Industrial valves
Industrial valves play a role in regulating the flow and checking the transfer of liquids in different systems, and depending on the type of material passing through and the nature of its application, it has different shapes and uses. Among the common valves in the oil and gas industry, the following can be mentioned:
- control valve
- Butterfly valve or butterfly valve
- Wing valve or ball valve
- Check valve or one-way valve
- Globe valve or spherical valve
The material of the used valves is determined according to the type of fluid passing through it. The material of the body can be steel, cast iron, steel 304, steel 316, Monel, etc., which should be selected according to the level of corrosiveness and other characteristics of the fluid.
6- Refinery furnaces
Refinery furnaces, which are also called furnaces, are equipment that are often used to heat gases or liquids entering refining systems and related equipment to the desired temperature.
Furnaces play a very important role in the petrochemical industry and refineries, whose accurate performance has a major impact on the efficiency and quality of the process unit, as well as its correct and economic performance, which is checked by the precision instruments unit in the refinery.
Design, implementation and operation of mini-refinery production units in the field of downstream oil industries
Foulad Machine Company having sufficient knowledge and review of its internal capabilities and having a direct relationship with international reputable companies that manufacture parts and devices while supplying the necessary devices and parts for production units in the oil sector.
Gas and Petrochemical has always tried to play an optimal and efficient role in the design and construction of mini-refinery units related to bitumen-oil-industrial solvent production projects and recycling systems related to used oil and refinery waste, Gas and Petrochemical has always tried to play an optimal and efficient role in the design and construction of mini-refinery units related to bitumen-oil-industrial solvent production projects and recycling systems related to used oil and refinery waste.
Some of these projects that have been designed, built and implemented in the production industries in the fields of bitumen-oil and petroleum solvents are as follows.
- Bitumen Oxidizer Tower (Batch Process & Continues Process )
- Atmospheric Distillation Unit
- Vacuum Distillation Unit
- Desulphurization Unit
- Blending Unit